.jpg&height=150&maxWidth=185)
History of Portadown Foundry
History of Portadown Foundry
Portadown Foundry Ltd F.S.A.Williamson
This is a rough history of Portadown Foundry Ltd from small beginnings in the mid nineteenth century through all sorts of changing times up until 1975. Throughout all those one hundred and some odd years, the foundry was in the forefront of developments in its line of business. It gained and has kept a reputation among Government Departments and its clients of producing a good ‘job’, keeping its delivery promises and looks forward to the next hundred years with confidence.
A Mr Woolsey began an engineering works in Foundry Street around 1844 (no relation of the Woolseys who later had a foundry in Francis Street in the Thirties). The site was that on which the present stores are built. The present office block was then a farmhouse, and the land between the Foundry and the railway was farmland.
At the bottom of Foundry Street was the sand quay, which still exists, and to the right of it was the original boathouse, belonging to Portadown Boat Club, a photo of which is in the Sprott collection.
Sometime in the late nineteenth century Portadown Foundry, as it was then known was taken over by the local family of Brights, and considerable investment was made. The farmhouse was acquired and modified as houses and four artisan houses, which were later demolished and rebuilt as the canteen.
About this period a patent was taken out for an enclosed type of safety pulley. It became very successful all over Ireland, being used to transmit power in the new mills then springing up. It was known amongst local wits as ‘Brights patent corned beef tin’. The manufacture of the pulley became the main product produced, and the name of the company was changed to ‘Brights Patent Pulley Company’.
In the early 1900’s a further investment was made, and leases were acquired for further pieces of land. A new foundry was built in the site of the boathouse, for the production of cast iron castings, with a small brass foundry attached. The contract for building the foundry was given to the late firm of Thomas Hyde & Sons ltd. The then new fitting shop, a three bay building, the smith’s shop and the new engine room were also built, and a new suction gas engine purchase and installed, the original engineering works being converted into stores and a pattern loft.
In the early 1900’s there was a big surge forward in the textile trade, and new factories were required. The foundry went into the construction business. The then very modern saw tooth roofs with north light glazing, to give natural light conditions, were beginning to appear. The method of construction was cast iron columns with cast iron valley beams that also formed the gutter between the north and south slope of the roof. The rest of the construction was usually of timber and glass.
This was a very big step forward at the time, from the previous types of dark and dismal factories. The columns were also made to carry the bearings for the line shafting, which transmitted the power from the steam engines to the various machines throughout the factory. The firm also patented a very advanced ring oil bearing to suit the line shafting being carried on the columns.
The main business at this time was the supply and erection of cast iron columns and beams for factory construction, the making of bearings, pulleys, couplings, etc., for the transmission of power in factories. The supply of replacement castings and fittings for the various machinery used in the factories. River Lighters were made using steel constructions, also, at this time an amount of castings were made for the numerous railway companies throughout Ireland.
During this period a start was made in structural steelwork, and several examples of hay sheds in the district bearing dates of 1906, 1910, existed until recent times.
The Foundry can also boast of having one of the first motorcar garages in Portadown. This was in Bridge Street where Mason’s hardware store now stands.
Mr Hamilton Rob who then owned a textile factory in Goban Street, started to experiment with building a motorcar in his workshop at his home, the former Portadown College buildings in Bridge Street. The Foundry made the ‘bits and pieces’ and supplied castings, but the project never went beyond the experimental stage.
So varied and busy was trade at this time that Bright Bros. Ran into financial trouble and a new company was formed with some of the linen firms taking an interest. Amongst the directors were Messrs. Spence, Bryson and Fulton, with Mr David Bright being appointed managing director; but still the financial troubles continued, and in 1911 Mr Bright resigned and went to America.
The Company advertised for a new manager and appointed Mr James A Williamson who had been works manager in Kane Bros. Foundries in Ballymena and Larne, and a teacher in engineering subjects in Ballymena and Carrickfergus Technical Schools.
Mr Williamson was not very happy with the set up as it was then, and in 1912 bought the share capital and re-formed the company with himself as chairman and managing director, his wife Mrs R Williamson and Mr Fred Allen, accountant, as directors. The name was then changed to the original Portadown Foundry Limited.
The commenced a period of expansion activities. The building of lighters was speeded up, including the installation of Bollinder and Gardner oil engines, and some of the old horse drawn lighters were converted to self-drive. The work for the railway companies was increased and the supply of rails and points undertaken. This included installing new machinery for the additional machining of rails and points. The garage and building contracting works was discontinued and all energies concentrated on the foundry and engineering departments,
The next important date was the start of the First World War in 1914. It is not generally realised that the number of aircraft produced by England during the first four years of the hostilities amounted to something like 60’000, all of which used vast quantities of linen, as the fuselage and wings were erected in all parts of Ireland from the North coast to Cork.
At the same time specialised castings for the railways, such as cylinder and piston, piston rings, funnels, blast pipe etc., which had previously come from England, became impossible to get, so the Foundry was expected to supply these. At the same time, thousands of mills bombs (hand grenades) were made and machined. This, together with supplying the various textile mills and other industries made the Foundry a very busy place during the war years.
The growing and processing of flax had been introduced to British East Africa (now Uganda/Kenya) during the 1914-1918 war, Portadown Foundry appointed Lamberts Limited, of London as their agents, during the early 1920’s large quantities of flax processing machinery was exported to Africa.
They also developed their agencies for Petters and Crosley engines. These were supplied and installed in small works and farms all over Ireland, for the supply of power and electricity.
In the early part of the century, Mr Dan Chapman had started up an electricity supply station at the rear of Jeffers’ shop in Market Street, and after the war the Foundry obtained for him, two diesel engines ex a German U-boat. These were installed at Market Street, and the starting up and training of staff were also undertaken, so it could be said that the Foundry had a hand in the starting up of the Electrical Supply Industry in Northern Ireland. The fishing fleets in Donegal and the West Coast of Ireland were converted to power about this time. The engines were supplied and fitted by the Foundry.
So continued the 1920’s until the general strike of 1926, and the world shattering events of 1928/29. The Foundry weathered the storm, although a large sum of money was lost through the sudden collapse of the African market and the run-down in home produced flax. Nevertheless, during 1928 a decision was taken to take advantage of the less busy times to bring the business up to date. The old suction gas engine, which had given such wonderful service was scrapped and replaced by a single cylinder Crossley diesel engine, and a new generator for the compressed air for riveting etc., were installed. A new engine house was used for general storage until replaced in 1938 by the present carpenter’s shop.
The old furnace was removed at the Foundry and a new larger furnace, staging and crane were erected. A new, very modern (for 1928) method for supplying the blast to the furnace was installed, this being a fan directly coupled to a D.C. motor, the current being from the work’s own supply.
An electric motor capable of taking over from the engine and using current from the public supply was also installed, but such was the cost of oil, that for a further ten years this was only used as a stand-by for the oil engine.
In 1928 Portadown got a complete new sewage scheme. The Foundry supplied all the cast iron road gullies etc.
A short lease of a portion of the farmland which Mr Green of Green’s mill, (now Heathwoods Store) used as a garden, was obtained when the mill closed. This consisted of a hill next to Watson Armstrong’s factory (now Wades) sloping down to swampland that was usually flooded during winter. The main entrance then, was where the workers entrance now is, and steel for the then embryo structural steelwork department was off-loaded on the street, stored up against the building, until it was man-handled into the works.
A more modern entrance and stock yard were badly needed, so when the then urban council demanded land to build a pumping station to pump sewage from the Edenberry area to the Seagoe Sewage Works, a deal was made with them that they would construct a new roadway down the side of the fitting shop, and the hill should be taken away in lieu of paying compensation. This was agreed and excavated material from the hill duly carted away by horse and cart and dumped beside the Bann Bridge, which then became the foundations for the Pleasure Gardens, between the river and the old Regal Cinema.
They then commenced dumping the waste sand from the foundry on the swampland, which, over the years, became the steel stockyard.
The thirties were a traumatic time for the Foundry. It was one of the very few Foundries in Ireland to weather the depression, and survive as a viable company. The African market had closed; textile factories were closing by the dozen. Portadown had at least twelve major factories and numerous small companies engaged in linen and associated trades at this times, now there are none. The Foundry never closed, but at times was down to a two or three day week.
There had always been a small agricultural department, making rickshifters, and hay collectors (tumbling paddies), also land-rollers. This was expanded; contracts were taken on for the Commissioners of Irish Lights, to make various complicated, but rarely profitable, parts for lighthouses around the coast of Ireland; with Belfast Harbour for the supply of castings, including mooring Bollards and machine parts.
The structural steelwork department was again expanded; in fact in the late twenties and thirties, the Foundry scored many notable firsts. A complete new factory at Ballievey, Banbridge, for Portman Textile Company was built. Incidentally, Portman went bust just before completion, so money was lost rather than made. The factory was then taken over by the Ballievey Bleaching Company. It was one, if not the first factory to be built in Northern Ireland, which had all structures made from structural steelwork. Even the chimney was steel, and was made in the Foundry.
The shopping arcade at North Street, Belfast was another large contract undertaken. A lot of sweat was lost in the works inventing a way to bend the rolled steel joists to form the attractive roof, seldom seen by shoppers. Have a look up next time you visit the arcade.
Numerous other buildings, including schools, telephone exchanges and libraries were built during this period, using steelwork supplied by the Foundry.
These may not seem great buildings now, but remember, in the early thirties, there was no electric welding, no mobile cranes, and even oxy-acetylene cutting was in its infancy.
At this time a lot of Cinemas were going up, but because of his religious convictions James A. Williamson, despite the shortage of work, would have nothing to do with ‘sin’ palaces or drink establishments. Another of his phobias was the introduction of allowances, on a limited scale, to sick or distressed families whose ‘men’ worked for the firm.
In the early thirties, to try and keep things moving, the one and only lorry the Foundry had was formed into a separate company with title Williamson & Co. Haulage Contractors, and a sister company with the same name title selling coal. The original idea was to use the spare time of the lorry to try and help out with some ready cash. It is happy to note that the company was highly successful and profitable in supplying coal to the brick companies in Dungannon and Coalisland with return loads of brick to Belfast and district; thus at the same time carting all the materials in and out of the Foundry at cost price.
This, notwithstanding the fact that James A’s religious convictions forced him to pay his drivers well over the standard rate for the district, plus a bonus, for working what would be called ‘unsocial hours’.
These two companies were wound up when the Haulage Company was nationalised in 1937.
Other work taken on at this time was gates and railings, a fine example of the craftsmanship of the workers can still be seen surrounding St.Marks Church in Portadown.
In spite of the depression and lack of profits, many improvements were made during this period and the company, which had been one of the pioneers of oxy-acetylene cutting, and welding of steel, in 1935 purchased and installed one of the first electric arc welding sets in Ireland. This was a 200 amp belt driven set, and many were the visitors and ‘spies’ who visited the works to see the wonders of steel being joined together by ‘sparks’, and who went away bewildered and to bathe sore eyes.
1937 was a very sad year for the company. After surviving the worst slump for many years, and beginning to see light at the end of a very dark tunnel, James A. died in March at the early age of fifty-six. His death introduced a period of uncertainty into the company.
Since 1912 James A. had been the life and soul of Portadown Foundry. He had brought on Robert J Magowan to the point of making him manager. His two brothers had joined him, Robert Williamson taking charge of the foundry and John Williamson the engineering side.
After long deliberations, his widow, Mrs Rebecca Williamson, decided to continue the good work, and the company again was reorganised.
Mrs Williamson became chairman, R.J. Magowan managing director, Robert Williamson works director, Miss Mary S Williamson director, John Williamson became work’s foreman, Tommy Uprichard Engineering foreman, John Harrison foundry and yard foreman, and last, but by no means least, James O’Neill was appointed structural steelwork foreman. Wilfred Sullivan, who had ‘served his time’ with the company as a pattern maker, and had been tutored by James A. in the design of structural steelwork, became designer and draughtman. James A’s son Fred S A Williamson joined the office staff at the ripe old age of fourteen.
The company then settled down to enjoy the fruits of improving times.
FROM THE NOTES OF F.S.A. WILLIAMSON
COURTESY KELSIE WILLIAMSON
|
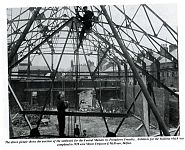
Portadown Foundry
Portadown Foundry
Photo courtesy of Rotary.
|
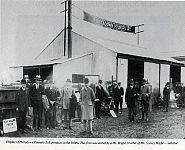
Poratdown Foundry
Poratdown Foundry
Photo courtesy of Rotary.
|